Untangling the Secret of Porosity in Welding: Tips for Decreasing Issues and Making Best Use Of Quality
In the complex globe of welding, porosity continues to be a persistent challenge that can substantially influence the top quality and honesty of bonded joints. As we delve into the midsts of porosity in welding, uncovering the secrets to its prevention and control will be critical for experts seeking to understand the art of high-quality weldments.
Comprehending Porosity in Welding
Porosity in welding, a common problem come across by welders, describes the presence of gas pockets or voids in the bonded material, which can jeopardize the honesty and quality of the weld. These gas pockets are usually caught throughout the welding procedure because of different elements such as incorrect securing gas, infected base products, or inaccurate welding specifications. The formation of porosity can weaken the weld, making it susceptible to splitting and corrosion, ultimately leading to architectural failings.
Comprehending the source of porosity is vital for welders to successfully prevent its incident. By acknowledging the significance of keeping appropriate gas shielding, ensuring the sanitation of base materials, and optimizing welding setups, welders can dramatically lower the possibility of porosity formation. Furthermore, utilizing strategies like preheating the base product, utilizing proper welding methods, and carrying out extensive evaluations post-welding can further assist in reducing porosity defects. Generally, a comprehensive understanding of porosity in welding is necessary for welders to create premium and durable welds.
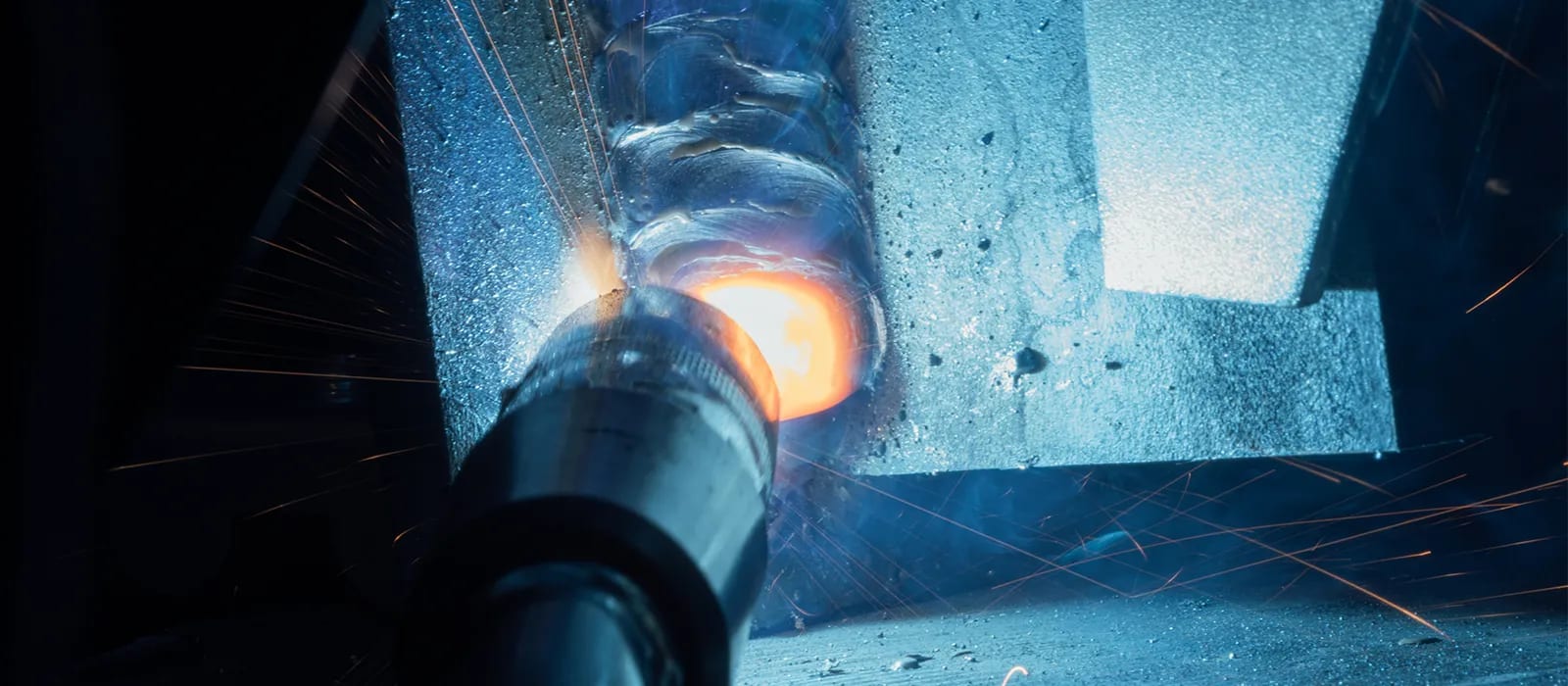
Typical Reasons For Porosity
When evaluating welding procedures for possible quality issues, understanding the common causes of porosity is essential for preserving weld stability and preventing architectural failings. Porosity, identified by the visibility of cavities or voids in the weld metal, can substantially jeopardize the mechanical homes of a welded joint.
Additionally, welding at improper specifications, such as exceedingly high traveling speeds or currents, can generate excessive turbulence in the weld swimming pool, trapping gases and creating porosity. By dealing with these usual reasons via correct gas shielding, material preparation, and adherence to optimal welding criteria, welders can reduce porosity and boost the quality of their welds.
Methods for Porosity Avoidance
Implementing reliable safety nets is vital in reducing the occurrence of porosity in welding processes. One strategy for porosity prevention is guaranteeing proper cleansing of the base metal prior to welding. Impurities such as oil, grease, corrosion, and paint why not try these out can cause porosity, so extensive cleansing using ideal solvents or mechanical techniques is essential.

Utilizing top notch filler materials and shielding gases that are appropriate for the base metal and welding process can substantially lower the danger of porosity. In addition, maintaining appropriate welding specifications, such as voltage, existing, take a trip rate, and gas flow rate, is important for porosity prevention.
Additionally, using correct welding strategies, such as keeping a consistent travel speed, electrode angle, and arc size, can help prevent porosity (What is Porosity). Sufficient training of welders to ensure they comply with finest techniques and top quality control treatments is additionally crucial in decreasing porosity problems in welding
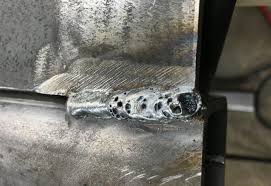
Ideal Practices for Quality Welds
Guaranteeing adherence to market requirements and correct weld joint prep work are essential aspects of achieving consistently high-grade welds. In enhancement to these foundational steps, there are numerous best techniques that welders can implement to even What is Porosity more enhance the quality of their welds. One secret technique is maintaining correct cleanliness in the welding location. Contaminants such as oil, oil, rust, and paint can detrimentally impact the high quality of the weld, causing problems. Completely cleaning the work surface and surrounding location prior to welding can assist minimize these issues.
An additional ideal technique is to thoroughly pick the ideal welding parameters for the certain products being signed up with. Proper parameter choice makes certain optimum weld penetration, fusion, and overall high quality. Utilizing high-grade welding consumables, such as electrodes and filler metals, can considerably impact the last weld quality.
Significance of Porosity Control
Porosity control plays a critical duty in making certain read the integrity and top quality of welding joints. Porosity, identified by the visibility of dental caries or gaps within the weld steel, can considerably jeopardize the mechanical buildings and architectural honesty of the weld. Too much porosity deteriorates the weld, making it much more susceptible to breaking, corrosion, and overall failure under functional tons.
Efficient porosity control is important for keeping the desired mechanical buildings, such as stamina, ductility, and durability, of the welded joint. What is Porosity. By reducing porosity, welders can enhance the general quality and integrity of the weld, guaranteeing that it satisfies the performance demands of the designated application
Additionally, porosity control is important for attaining the desired visual appearance of the weld. Too much porosity not only deteriorates the weld however also interferes with its aesthetic charm, which can be critical in industries where aesthetics are necessary. Correct porosity control techniques, such as using the appropriate protecting gas, regulating the welding criteria, and guaranteeing correct cleanliness of the base products, are essential for creating high-quality welds with very little issues.
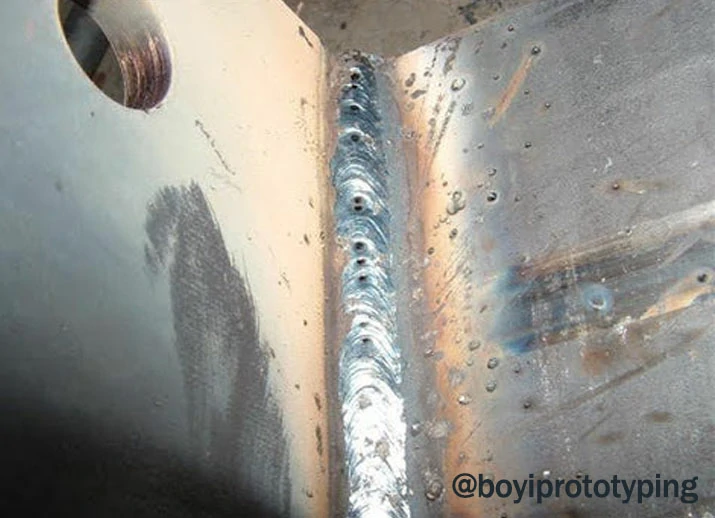
Verdict
To conclude, porosity in welding is an usual problem that can jeopardize the quality of the weld. By comprehending the sources of porosity and applying proper prevention techniques, welders can decrease problems and achieve greater quality welds. It is important to regulate porosity in welding to guarantee the stability and stamina of the end product. Carrying out ideal practices for porosity control is critical for accomplishing optimal welding results.